精密加工のためのあらゆる加工手段を揃えて、
高精度化が要求される車載分野や
半導体・電子デバイス用部品の品質安定をご提案いたします。
目的の部品加工のための委託工場を探される場合、時間と労力がかかると思います。
弊社ではそのようなお悩みを感じていただくことがないように、
金属の精密加工における大半の加工をカバーできる体制を設けております。
主な対応加工手段
- プレス加工
- 切削加工(フライス・マシニング)
- レーザー加工(抜き)
- ベンダー(曲げ)加工
- ワイヤー(抜き)加工
- 簡易プレス(曲げ)(絞り)
- 洗浄(スポット少量対応)
- めっき(スポット少量対応・希少なめっき)
- エッチング
- 放電加工
調達・加工実績のある主な素材
- 銅(C1020R・C1100R・TAMAC2 1/2H・TCUP1/4等)
- アルミ(ALP1100・ALP1050等)
- 42アロイ(42Ni-Fe)
- りん青銅(C5191R等)
- 真鍮(C2680R・C2801P等)
- ステンレス(SUS303・SUS304等)
- 鉄(SPCC・SPHC等)
- その他
OUR TECHNOLOGY精密加工のポイント
薄くて複雑形状の曲げ加工や、傷が許されない光沢メッキなど
品質管理が難しいとされる部品であっても高精度で加工
薄くて複雑形状の曲げ加工や、傷が許されない光沢メッキなど一見精度を保つのが難しい加工品においても、弊社の品質管理能力が発揮されます。実際の加工時の問題点をあらかじめ予想できる経験とノウハウをもった技術者が、要求される精度を確保できる最適な加工条件の下ご提案し、加工を行います。
基本的な品質管理における精度向上、部品反り防止対策等はもちろんのこと、工場内・機械の温度管理、振動対策等の環境管理も欠かしません。
精密電子部品製造で培ったノウハウを最大限に発揮いたします。
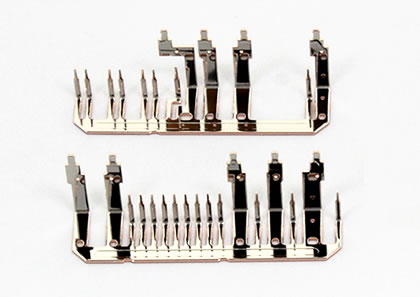
目先の精度だけでなく、量産時の精度安定や
トータルコストを踏まえた加工体制
何事もゴールからの逆算といいます。それは加工であっても同じこと。1個だけ精度が高くとも、量産になった途端精度がばらついてはいけませんし、コストがかかりすぎてもだめでしょう。その部品が最終どうなるのかを見据えた精密加工が市場の信頼へとつながると考えております。
例:プレス加工における精密加工工程
1.ご提案
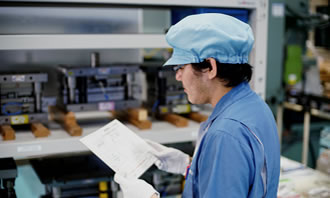
- お客様からいただいた図面を弊社内で確認いたします。
- 指定素材の有無等を確認し、希少性コストアップ・調達困難さ等がある場合、相当品でのコスト・入手し易さ等をご提案。
- 寸法・精度の必要箇所、その逆に図面には記載されているが、精度の緩い箇所を確認し、最適な加工方法を選定。
- また、同時に最大生産数を確認し、コストにあった加工方法を選定いたします。
2.試作品製作
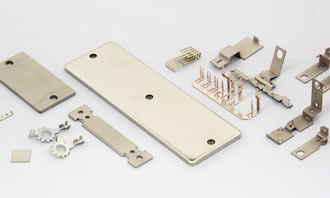
試作金型・切削等の手段により試作を行います。
図面をもとに実際の加工を行うことで見えてくる問題点等をフィードバックし、調整を加えていきます。完成後はお客様にて試験を行っていただき、問題点があれば改良を加えていきます。
3.金型設計・製作
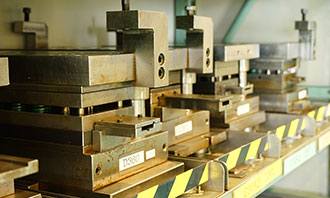
製品精度、大きさにもよりますが、可能であればブランク(製品+スクラップ)を最小限に抑制するレイアウト(取り方)を提案します。加工方法が複雑化すると金型費がアップする為、お客様と協議し、加工方法を間引き、金型コスト抑制を行ないます。
また板厚と加工方法(精度の高さ)等にもよりますが、生産数が少ない場合、安価な金型材質を提案し、金型コストの抑制を計ります。
4.精密プレス加工
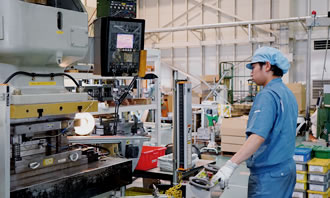
板厚0.5mm~6mmについては社内対応可能です。それ以下もしくはそれ以上の場合、協力会社様にて加工(最終品質は弊社で保証いたします)。また多列化、プッシュバック方式等によるコストダウン・品質アップの方式も得意分野です。
5.脱脂洗浄
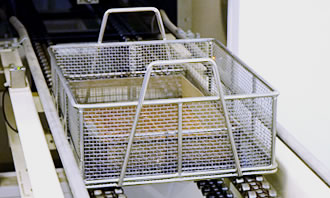
臭素系洗浄用溶剤で、塩化メチレン、トリクロロエチレン等の塩素系溶剤に匹敵する洗浄性能を持っています。さらに、不燃性、低毒性、速乾燥性等の特徴を有していますので、金属加工部品、電子部品、精密部品及びセラミック・ガラス等の脱脂洗浄が、安全に効率良くできます。
6.めっき加工
- 製品の大きさ・精度・お客様からのご要望等により、めっき方法(つり、フープ・バレル等)を選定いたします。
- 試作の場合、ロットが少量であれば手付けもあります。
- 製品の仕様によっては、2種類のめっき、部分めっきも対応いたします。
- 取扱めっきの種類については、仕様・生産数等要望によりめっき会社を選定いたします。
7.レジスト印刷
半導体用レジスト印刷が主です。製品の仕様(レジスト位置・範囲等)により対応可否を検討いたします。
8.検査
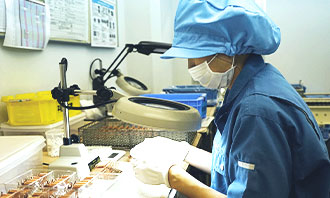
半導体ICで培った目、管理方法で流出を防止するだけでなく、前工程へフィードバックする事により発生対策を行ないます。
またQLC(Quality Level Check)、MQC(Machine Quality Control)を実施し、予防保全も行なっております。